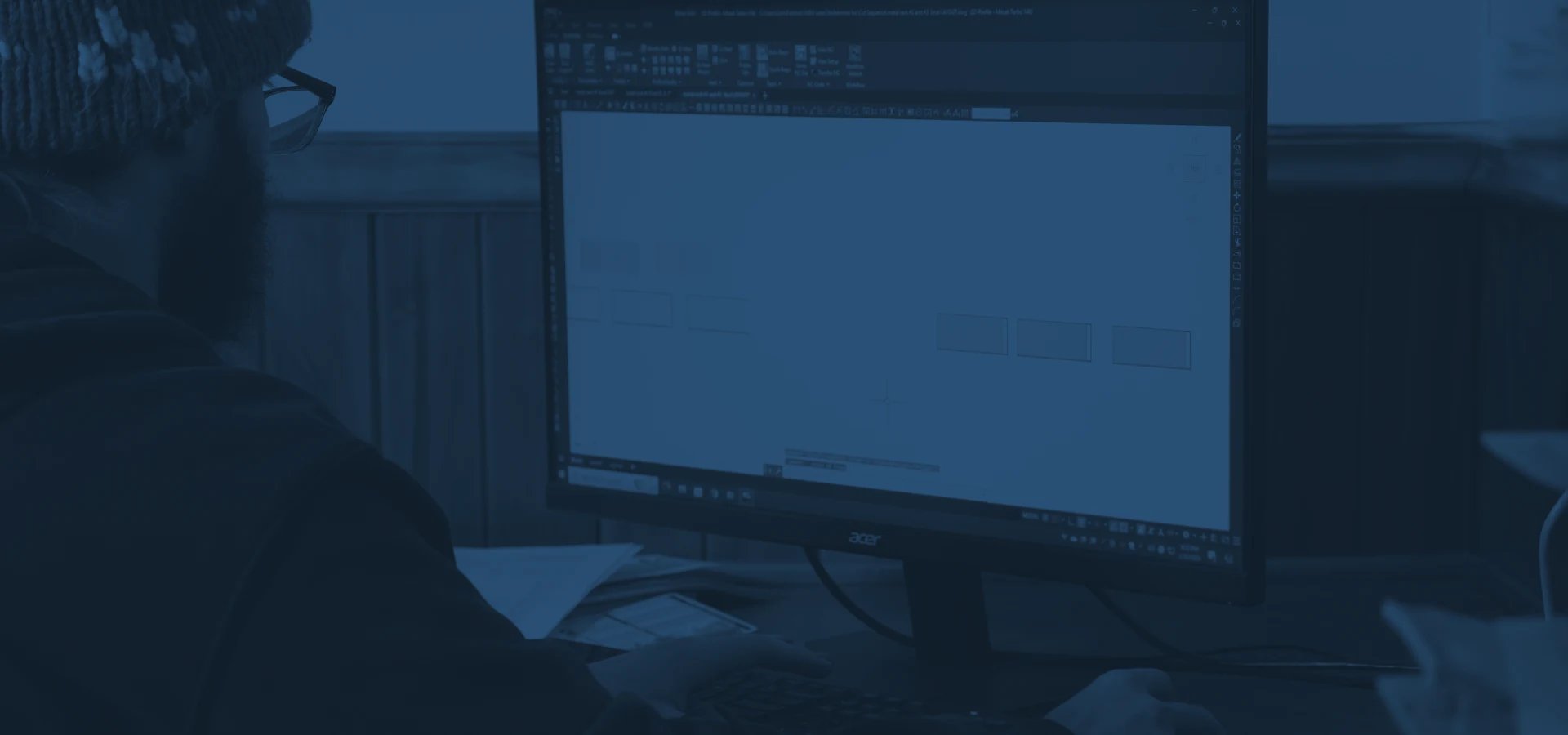
OUR PROCESS
CUSTOM SOLUTIONS
As a customer of our local metal fabrication shop, you can expect a seamless experience tailored to your specific needs. From initial consultation to final delivery, we prioritize clear communication, quality craftsmanship, and timely completion.
Design and Planning:
Our team will work closely with you to develop detailed plans and renderings. Whether you have a precise design in mind or need assistance in conceptualizing your project, we're here to offer expert guidance.
Consultation:
Upon reaching out to us, you'll be welcomed with a personalized consultation. We'll discuss your project requirements, specifications, and budget to ensure we fully understand your vision.
Material Selection:
We offer a wide range of high-quality materials, including mild steel, galvanized steel, pre-finished steel, stainless steel, aluminum, and copper to suit your project's unique requirements. Our knowledgeable staff will help you select the most suitable material based on factors such as strength, durability, and appearance.
Fabrication Process:
Once the design and materials are finalized, our experienced fabricators will execute your project using advanced equipment and techniques. Whether it's precision laser cutting, welding, or forming, we adhere to the highest standards of quality.
Progress Updates:
Throughout the fabrication process, we'll keep you informed of progress milestones and any adjustments made to the project timeline. Transparency and communication are key to ensuring your satisfaction every step of the way.
Quality Assurance:
Before final delivery, each piece undergoes quality checks to ensure it meets our standards. From dimensional accuracy to surface finish, we leave no detail overlooked.
Pick Up, Delivery, or Installation:
Upon completion, we'll contact you for pick up or coordinate the delivery and, if required, installation of your project. Our goal is to ensure a smooth and hassle-free experience, leaving you with a finished product that exceeds your expectations.
Your satisfaction is our top priority. We value your feedback and are committed to addressing any concerns or issues promptly and effectively.
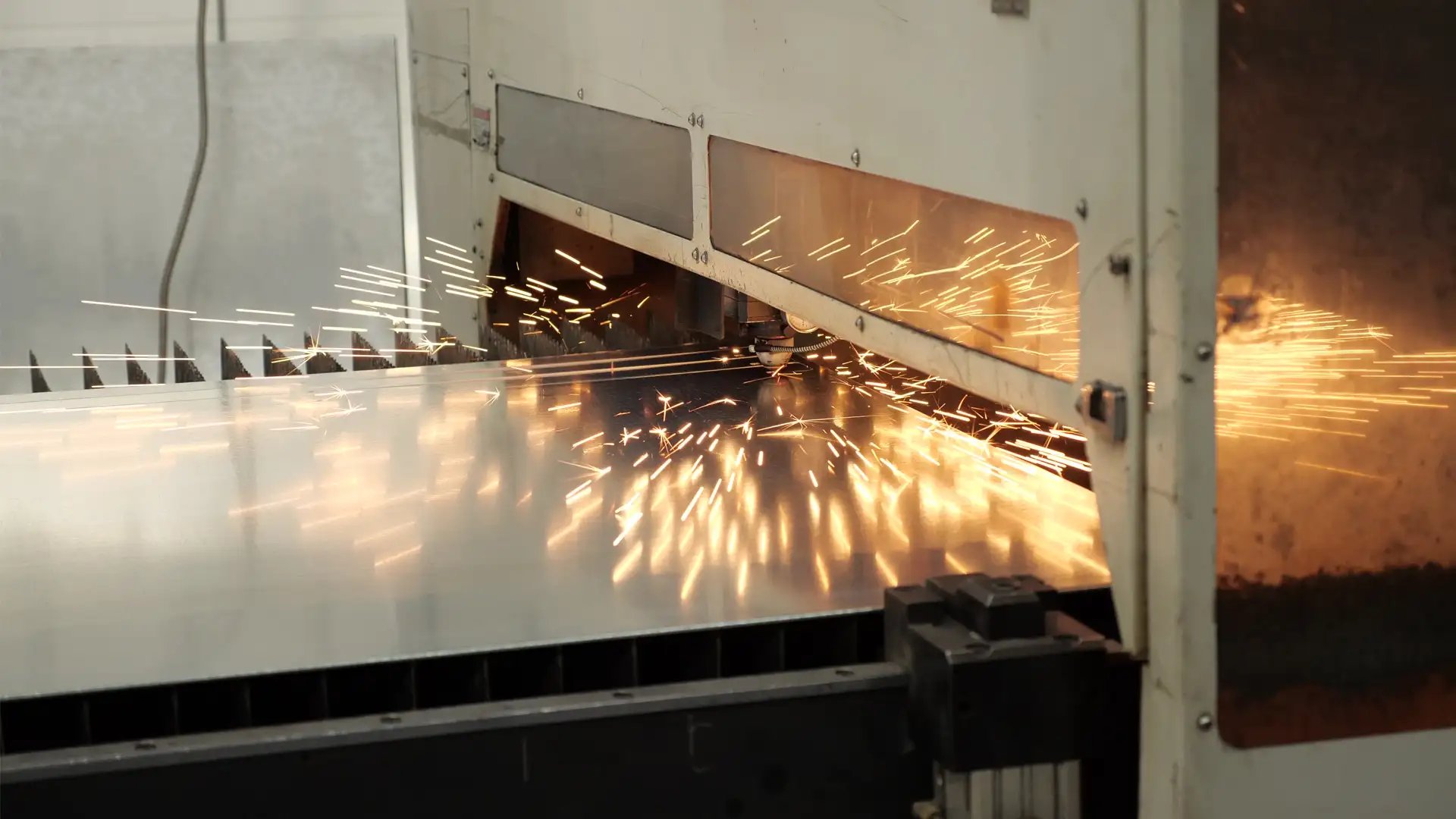
Over 20 years of trusted manufacturing experience working for you
CUSTOM SOLUTIONS
Each customer’s project that we make is unique. Here are some examples to show a general process of what you can expect.
Custom Order Example #1
A guest arrives to our shop in need of a new part to get their equipment back up and running. The old part is brought in and rusted out. It’s approximately 26”x18”x4” in size and made out of 1/16” sheet metal. Multiple bends are needed for side walls and holes and attachment points at exact locations need to be replicated.
We’ll assess the needs and offer solutions such as better material to be used like stainless steel. Then make sketches and take measurements of all important areas to be fabricated.
At this point we have a good estimate of lead time and cost. If the estimate is approved we’ll proceed in producing final drawings in CAD.
The sketches then turn into a final CAD drawing which then gets prepared for cutting on our laser machine. If the chosen material is in stock, the programmed drawing can be cut out of the flat sheet of metal.
This cutout will then be transferred to our other machinery to finalize the form according to all specifications.
The customer is contacted and the project is now ready to be picked up.
The lead time for this project was: {2-3} days
Price range: $$ Cost varies widely for custom builds.
Custom Order Example #2
We receive a call from a local building contractor who has a customer in need of a custom outdoor kitchen for their home. They need multiple custom builds including a range hood, counter top and doors…(?). Each component has different sizes {and materials} with multiple fabricating steps involved for each. The contractor is in charge of installation.
We’ll assess the needs of this large scale project and offer solutions such as material to be used and also finishing options for design goals. On-site visits will take place to get measurements and discuss any structural concerns. Ongoing communication will happen with the contractor as the project progresses and the homeowner may or may not be directly involved with collaborating on the project.
Photos will be taken on-site, sketches will be made for each component, and measurements of all important areas recorded. We can then have the ability to send the contractor a visual mockup of the intended final project.
At this point we have a good estimate of lead time and cost. If the estimate is approved we’ll proceed in producing final drawings in CAD.
The multiple sketches then turn into final individual CAD drawings which then get prepared for cutting on our laser. Depending on availability of the chosen materials, we will work directly with our metal suppliers to receive the best options at the best prices.
We will begin laser cutting and other fabrication processes according to all specifications.
The customer is contacted and the project is now ready to be picked up.
The lead time for this project was: {3-4} months
Price range: $$$$ Cost varies widely for custom builds.
As a customer of our local metal fabrication shop, you can expect a seamless experience tailored to your specific needs. From initial consultation to final delivery, we prioritize clear communication, quality craftsmanship, and timely completion.